Your Trusted Partner in Oil, Gas, Petrochemical, and Other Industrial Supplies
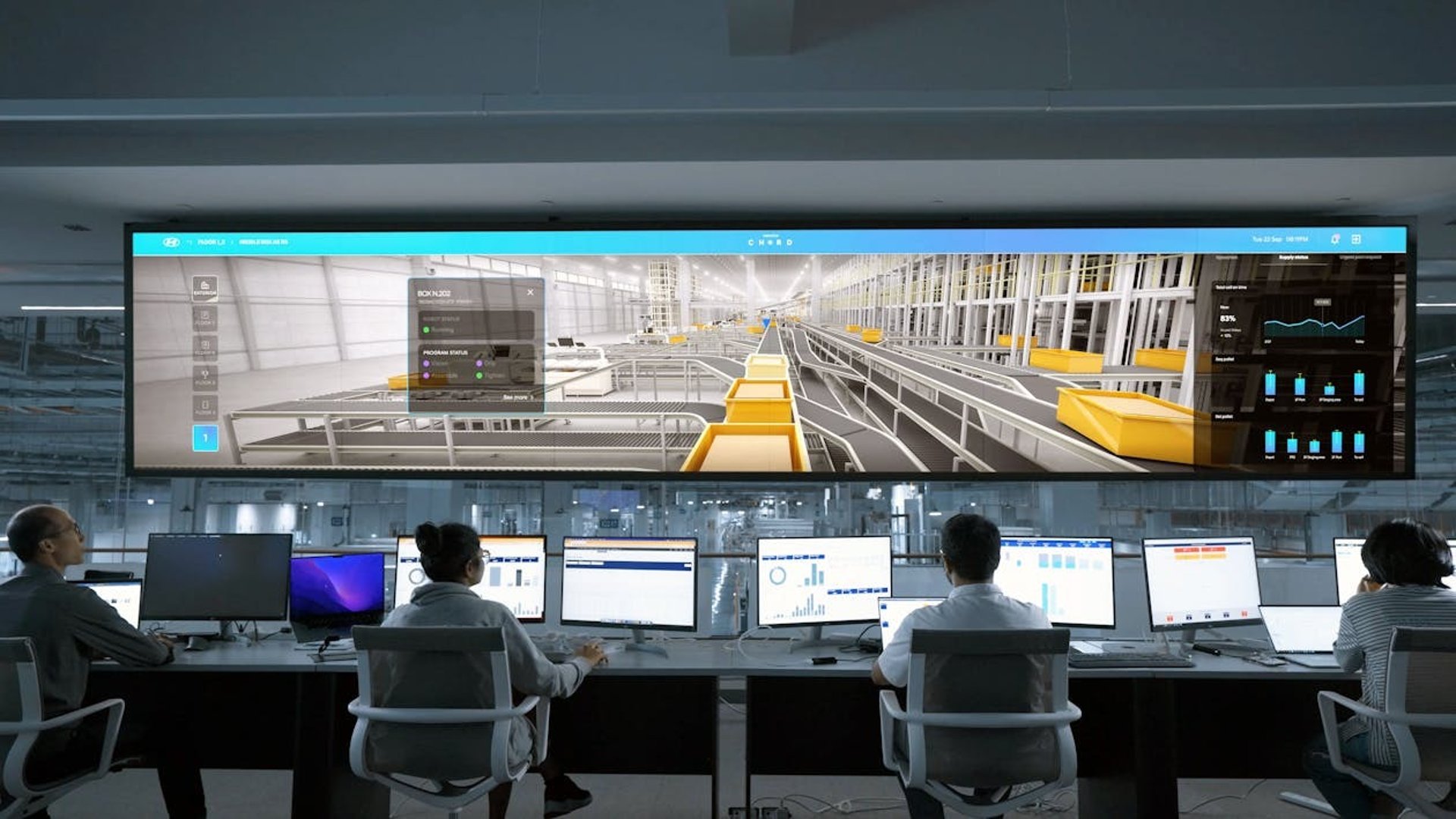
Instrumentasi : Sistem Kontrol, Transmisi Data, dan Sinyal Instrumen
Pernahkah Anda bertanya-tanya bagaimana pabrik-pabrik besar bisa berjalan otomatis tanpa campur tangan manusia? Di dunia industri proses—dari minyak dan gas hingga makanan dan minuman—semuanya bergantung pada pengendalian parameter seperti aliran, tekanan, level, dan suhu. Tapi, apa yang membuat sistem kontrol otomatis lebih unggul dari kontrol manual? Dan bagaimana peran sinyal instrumen dalam memastikan setiap proses berjalan lancar? Temukan jawabannya di sini, termasuk perbedaan mendasar antara kontrol loop terbuka dan loop tertutup!
1/17/20256 min read
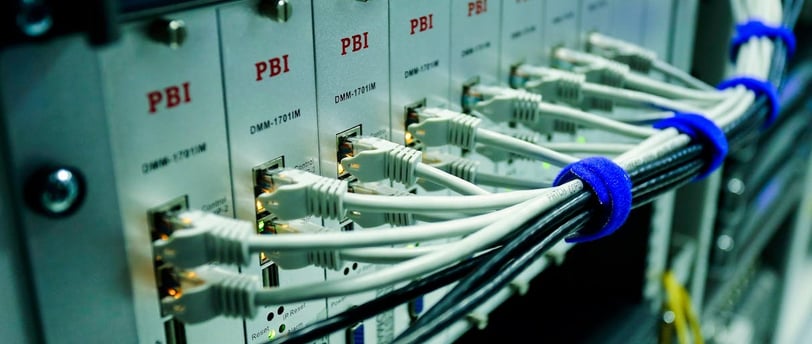
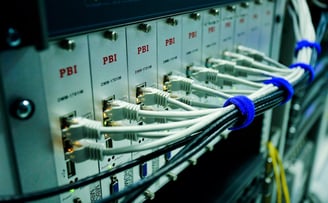
1. Sistem Kontrol
Industri proses mencakup berbagai sektor seperti minyak dan gas, petrokimia, farmasi, makanan dan minuman, hingga pembangkit listrik, yang semuanya bergantung pada pengendalian parameter fisik seperti aliran (flow), tekanan (pressure), level, dan suhu (temperature). Monitoring dan pengendalian parameter ini penting untuk menjaga proses berjalan secara stabil, efisien, dan aman. Proses ini melibatkan perangkat instrumentasi seperti transmitter untuk mengukur parameter fisik, converter untuk mengubah sinyal menjadi format tertentu, indicator untuk menampilkan data, controller untuk mengatur jalannya proses, recorder untuk mencatat data operasional, dan control valve sebagai elemen pengendali akhir. Kombinasi perangkat ini memungkinkan pengelolaan yang terintegrasi sehingga kondisi operasi dapat dipantau dan dikendalikan secara optimal. Jenis sistem kontrol pada instrumentasi dibedakan menjadi dua yakni open loop system dan closed loop system.
Pada sistem lingkar terbuka (open loop system), monitoring dilakukan tanpa kemampuan kontrol otomatis. Sistem ini hanya mengukur dan menampilkan parameter fisik tanpa mekanisme untuk mengoreksi kondisi yang menyimpang dari target. Contoh sederhana dari aplikasi sistem lingkar terbuka adalah pemantauan level air pada tangki penyimpanan. Transmitter mengukur ketinggian air dan data tersebut ditampilkan melalui indicator atau recorder. Jika level air terlalu rendah, operator akan secara manual membuka katup untuk menambah air ke dalam tangki. Sistem ini cocok untuk aplikasi sederhana atau situasi di mana intervensi manual sudah cukup untuk menjaga proses tetap berjalan.
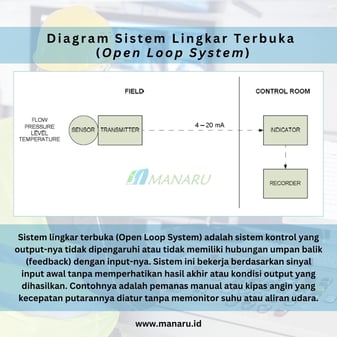
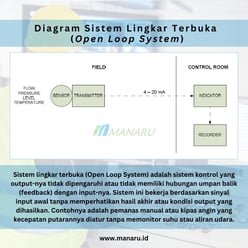
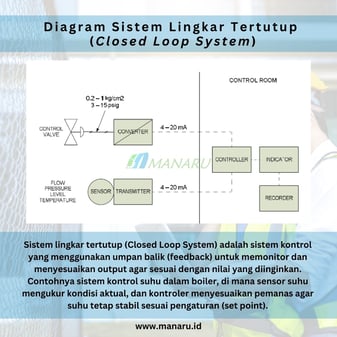
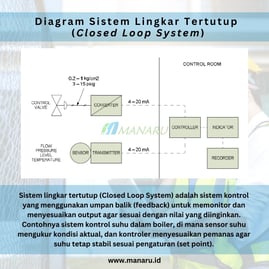
Sebaliknya, sistem lingkar tertutup (closed loop system) dirancang untuk tidak hanya memonitor, tetapi juga mengontrol parameter agar tetap sesuai dengan nilai target (set point) secara otomatis. Sistem ini menggunakan controller untuk membandingkan data aktual dengan set point, kemudian memberikan perintah kepada elemen kontrol, seperti control valve, untuk menyesuaikan proses. Contoh nyata aplikasi sistem lingkar tertutup adalah pada sistem pemanas air di boiler. Suhu air diukur oleh transmitter dan data tersebut dikirim ke controller. Jika suhu aktual lebih rendah dari set point, controller akan menginstruksikan control valve untuk meningkatkan aliran bahan bakar ke burner, sehingga suhu naik ke tingkat yang diinginkan. Sistem ini sangat penting untuk aplikasi yang membutuhkan stabilitas, presisi tinggi, dan respons cepat terhadap perubahan kondisi proses.
2. Instrument Signal Transmission
Transmisi data adalah proses pengiriman informasi berupa besaran fisik yang telah diukur, seperti aliran (flow), tekanan (pressure), ketinggian (level), atau suhu (temperature), dari lokasi pengukuran (misalnya di area plant) ke lokasi lain yang biasanya berjarak jauh, seperti ruang kontrol (control room) dalam suatu industri. Proses ini memungkinkan data yang dikirim untuk digunakan dalam berbagai tujuan, yaitu:
Displaying (Menampilkan): Data yang dikirimkan ditampilkan pada perangkat seperti monitor atau panel indikator di ruang kontrol. Dengan ini, operator dapat memantau kondisi proses secara real-time tanpa harus berada di lokasi pengukuran.
Recording (Merekam): Data yang diterima dapat dicatat atau direkam menggunakan perangkat seperti recorder digital atau analog. Hal ini berguna untuk keperluan dokumentasi, analisis performa, atau pelaporan operasional.
Controlling (Mengendalikan): Data yang diterima digunakan untuk pengendalian proses secara otomatis. Contohnya, jika suhu melebihi batas yang diinginkan, sistem kontrol dapat mengirim perintah untuk menyesuaikan pengaturan, seperti membuka atau menutup katup.
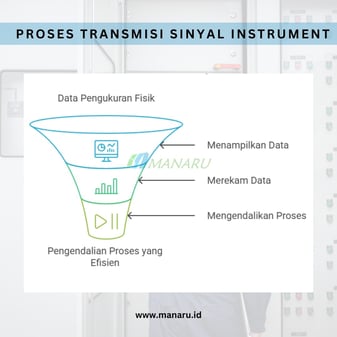
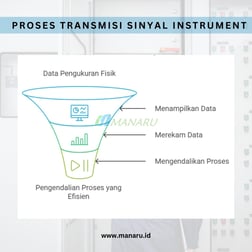
3. Media Transmisi
Pengiriman data (data transmisi) dalam industri dilakukan menggunakan berbagai media, yaitu tubing, kabel, dan serat optik (fiber optic). Setiap media memiliki prinsip kerja dan keunggulan yang berbeda sesuai dengan kebutuhan aplikasi. Berikut penjelasan lebih rinci:
Media Tubing (Transmisi Pneumatik)
Transmisi data dengan tubing (pneumatik) memanfaatkan perubahan tekanan udara (3–15 psig atau 0,1 hingga 1 kg/cm²) sebagai media pengiriman informasi. Metode ini sederhana dan cocok untuk lingkungan berisiko tinggi terhadap gangguan listrik, seperti area berbahaya. Namun, keterbatasan jarak dan respons waktu membuatnya kurang ideal untuk aplikasi berkecepatan tinggi atau presisi tinggi.Media Kabel (Transmisi Elektrik)
Pengiriman data melalui kabel adalah metode umum dalam industri proses, menggunakan besaran elektrik seperti arus 4–20 mA yang tahan gangguan dan cocok untuk jarak jauh, serta tegangan 1–5 V DC untuk aplikasi sederhana. Data kompleks dapat dikirim melalui modulasi frekuensi atau pulsa. Media kabel juga mendukung teknologi seperti HART dan Foundation Fieldbus untuk pengiriman data tambahan dan diagnostik.Media Fiber Optic (Transmisi Cahaya)
Transmisi data dengan serat optik menggunakan cahaya untuk mentransmisikan sinyal, yang tahan terhadap gangguan elektromagnetik. Kelebihan utamanya adalah kemampuan mentransmisikan data dalam jumlah besar dengan kecepatan tinggi, stabilitas, dan jarak jauh tanpa kehilangan sinyal. Fiber optic ideal untuk aplikasi yang membutuhkan kecepatan dan keamanan tinggi, seperti di pabrik besar atau jaringan komunikasi industri.
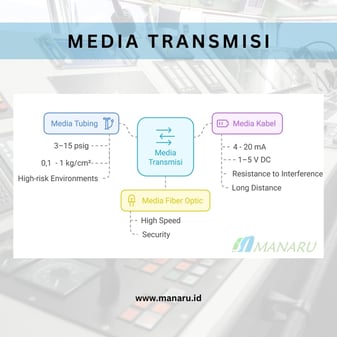
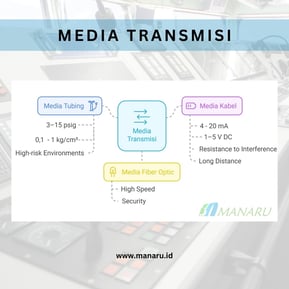
4. Jenis Sinyal Instrumen
Beberapa standar sinyal instrumen yang didefinisikan oleh asosiasi standar atau standar proprietari terbagi menjadi dua kategori utama, yaitu sinyal analog dan sinyal digital.
Sinyal Analog
Sinyal analog yang umum digunakan meliputi sinyal pneumatik, yang beroperasi pada rentang tekanan 3 hingga 15 psig (0.2 – 1 kg/cm²), 20 hingga 100 kPa, atau 6 hingga 30 psig. Selain itu, sinyal analog juga bisa berbentuk tegangan, dengan variasi seperti 1 hingga 5 V DC, 0 hingga 5 V DC, atau 0 hingga 10 V DC. Sinyal arus juga banyak digunakan, dengan rentang yang meliputi 4 hingga 20 mA, 8 hingga 40 mA, atau 10 hingga 50 mA.
Sinyal Digital
Terdapat beberapa protokol komunikasi yang sering diterapkan antara lain: HART Protocol, SMAR Protocol, Fieldbus, Modbus, Profibus, dan Industrial Ethernet. Selain itu, perkembangan teknologi komunikasi tanpa kabel (wireless communications) juga semakin populer dalam sistem instrumen industri.
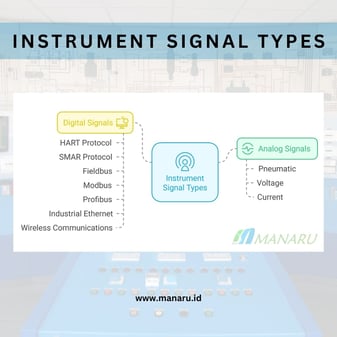
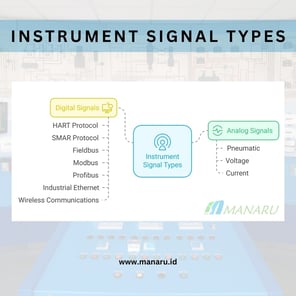
5. Pemilihan Sinyal Instrumen
Sinyal keluar dari transmitter, baik analog (pneumatik atau elektrik) maupun digital (seperti HART, SMAR, atau Fieldbus), umumnya bekerja dalam rentang skala tertentu. Untuk aplikasi industri proses, sinyal pneumatik biasanya menggunakan skala 3–15 psig atau 0.2–1 kg/cm², sedangkan sinyal elektrik yang sering digunakan adalah 4–20 mA (sinyal arus) atau 1–5 V DC (sinyal tegangan). Misalnya, sinyal arus 4–20 mA banyak diterapkan dalam pengukuran aliran dan tekanan pada berbagai sistem industri karena kemampuannya untuk mengurangi gangguan sinyal. Sebagai contoh, pada industri pengolahan air, sinyal 4–20 mA digunakan untuk mengukur aliran air dalam pipa besar. Transmitter arus ini mengubah perubahan aliran menjadi sinyal 4–20 mA yang kemudian diteruskan ke kontrol sistem, yang mengatur pompa untuk menjaga aliran tetap stabil.
Pada industri kimia, sinyal yang sama digunakan untuk pengukuran tekanan dalam sistem reaktor. Transmitter tekanan dengan sinyal 4–20 mA memberikan data real-time kepada sistem kontrol untuk menjaga tekanan dalam batas aman, menghindari overpressure yang dapat menyebabkan kecelakaan. Keunggulan dari sinyal 4–20 mA ini adalah kemampuannya untuk mentransmisikan data jarak jauh dengan ketahanan terhadap gangguan listrik, menjadikannya ideal untuk aplikasi di pabrik kimia atau pembangkit listrik.
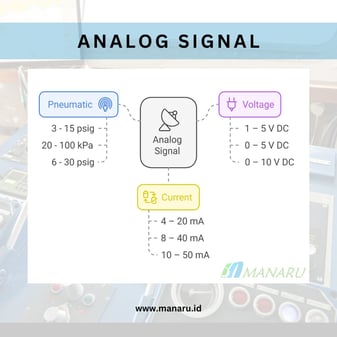
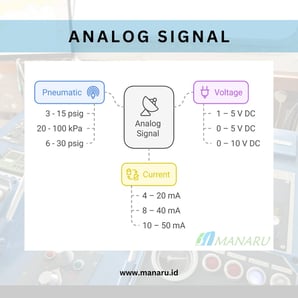
Pada transmisi sinyal elektrik, kawat tembaga dengan diameter antara 1.5 hingga 2.5 mm digunakan, seperti pada sistem kontrol suhu di pabrik kimia. Sedangkan untuk sinyal pneumatik, tubing dengan diameter 0.25 inci (atau 0.375 inci untuk beberapa aplikasi) digunakan, seperti pada sistem kontrol aliran di industri minyak dan gas. Pemilihan material tubing sangat bergantung pada kondisi lingkungan. Contohnya, tubing tembaga tidak cocok digunakan di ladang minyak lepas pantai karena udara laut yang korosif, sementara tubing plastik tidak akan bertahan di area dengan suhu tinggi seperti di dapur (furnace) karena mudah meleleh.
Dalam perkembangan teknologi, banyak sistem kontrol kini menggunakan komunikasi digital dan perangkat komputer. Beberapa instrumen juga memanfaatkan komunikasi melalui sinyal radio atau serat optik. Misalnya, sensor suhu atau tekanan dalam sistem kontrol otomatis di pembangkit listrik sering menggunakan komunikasi digital melalui protokol seperti HART atau Modbus. Namun, jenis sinyal ini lebih spesifik dan tidak memiliki standar umum, karena sangat bergantung pada sistem unit elektronik yang digunakan, yang memberikan fleksibilitas dalam komunikasi data di industri modern.
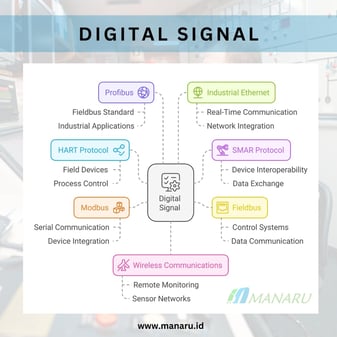
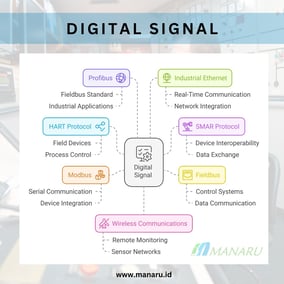
Summary
Industri proses seperti minyak dan gas, petrokimia, dan pembangkit listrik sangat bergantung pada sistem kontrol yang presisi untuk menjaga stabilitas, efisiensi, dan keselamatan operasional. Sistem ini memanfaatkan teknologi pengukuran dan transmisi data dengan berbagai media seperti tubing, kabel, dan serat optik, yang mendukung pengiriman sinyal analog maupun digital. Dengan protokol komunikasi seperti HART, Modbus, dan Fieldbus, serta pemilihan sinyal yang tepat seperti 4–20 mA, sistem mampu memberikan monitoring dan kontrol yang andal. Teknologi modern, termasuk komunikasi digital dan nirkabel, semakin meningkatkan fleksibilitas dan efisiensi dalam pengelolaan data dan proses, menjadikan sistem kontrol otomatis sebagai tulang punggung industri modern yang membutuhkan akurasi dan respons cepat.
Baca Juga
Menyingkap Rahasia Pengukuran Suhu: Dari Termometer hingga Pyrometer
Pengukuran Tekanan (Pressure Measurement) : Pengertian, Prinsip Kerja, dan Alat Ukur
Mengenal Beragam Metode Pengukuran Level Fluida untuk Industri Modern
Memahami Prinsip dan Teknologi Pengukuran Aliran Fluida (Flow Measurements)
Instrumentasi dan Pengendalian Proses
Memahami Sistem Instrumentasi: Tulang Punggung Industri Minyak, Gas, dan Petrokimia
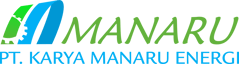
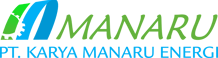
SOCIAL MEDIA
OFFICIAL STORE
We offer solutions to customers in need of quality equipment for the industry.
CATEGORY
Instrumentation
Valve
Fitting & Flange
Electrical
General Trading for Project
PT. Karya Manaru Energi
Kirana Two Office Tower, Lantai 10A, Jl. Boulevard Timur No.88
Pegangsaan Dua, Kelapa Gading, Jakarta Utara
DKI Jakarta - 12450
MARKETING OFFICE
© 2025 PT. Karya Manaru Energi.
All Right Reserved