Your Trusted Partner in Oil, Gas, Petrochemical, and Other Industrial Supplies
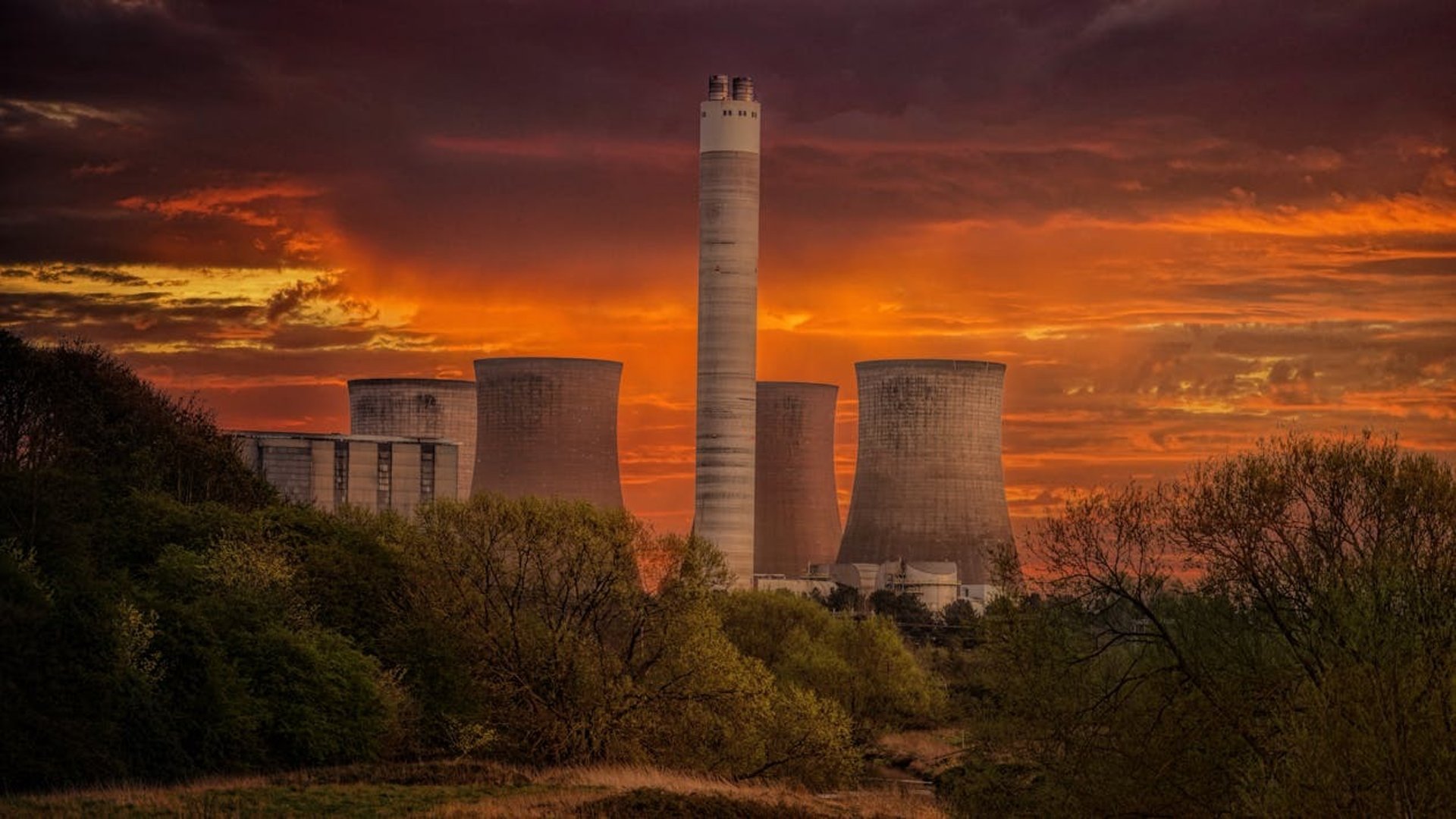
Instrumentasi dan Pengendalian Proses
Instrumentasi adalah seni dan ilmu yang mengaplikasikan alat ukur dan sistem kontrol untuk memantau dan mengatur suatu proses. Sedangkan Sistem pengendalian proses adalah suatu sistem yang dirancang untuk memantau dan mengontrol variabel-variabel yang ada dalam suatu proses industri agar tetap berada dalam kondisi yang diinginkan atau optimal.
11/30/20246 min read
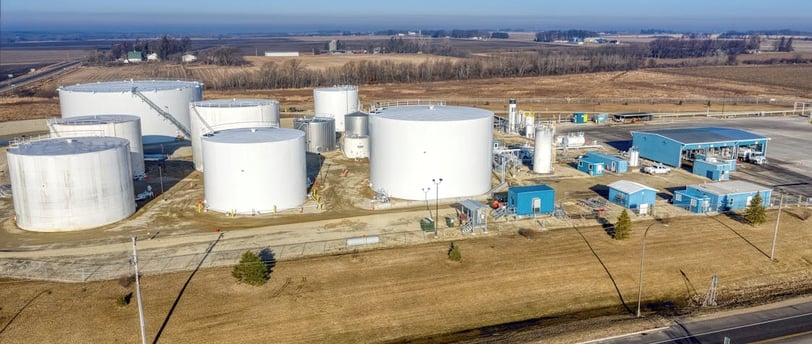
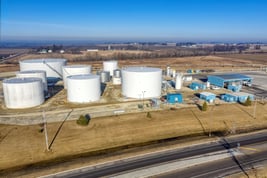
Dalam dunia industri, berbagai proses terjadi secara terus-menerus untuk menghasilkan produk atau layanan yang diinginkan. Proses-proses ini sering kali melibatkan serangkaian langkah yang kompleks, mulai dari pemrosesan bahan mentah hingga pengolahan akhir. Setiap langkah dalam proses tersebut memerlukan pemantauan yang cermat untuk memastikan bahwa hasil akhirnya sesuai dengan standar yang ditetapkan. Untuk mencapai hal ini, alat dan teknologi yang tepat diperlukan untuk mengukur dan mengendalikan variabel yang mempengaruhi proses tersebut. Di sinilah peran instrumentasi sangat penting. Instrumentasi tidak hanya mengukur, tetapi juga memungkinkan pengendalian dan pemantauan secara real-time, sehingga proses dapat dijalankan dengan efisien dan aman.
1. Pengertian Instrumentasi
Instrumentasi adalah seni dan ilmu yang mengaplikasikan alat ukur dan sistem kontrol untuk memantau dan mengatur suatu proses. Tujuannya adalah untuk mengukur nilai variabel proses secara akurat dan menjaga agar nilai tersebut tetap berada dalam batas yang ditentukan atau mencapai nilai yang diinginkan (set point).
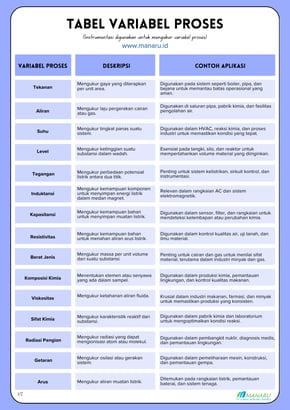
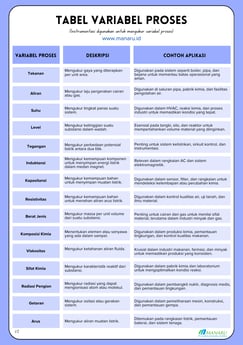
2. Contoh Aplikasi Instrumentasi
Dalam industri ada beberapa variabel proses yang diukur dan dikendalikan. Aliran (flow) merupakan salah satu variabel proses berupa laju pergerakan cairan atau gas dalam sistem, misalnya aliran minyak mentah atau gas alam yang mengalir melalui pipa untuk memastikan distribusi yang efisien dan aman. Tekanan (pressure) merupakan besarnya gaya yang bekerja di setiap satuan luas permukaan, misalnya pada vessel - tekanan diukur untuk mencegah tekanan berlebih yang bisa menyebabkan kebocoran atau kerusakan. Suhu (temperature) merupakan ukuran tingkat panas atau dingin suatu sistem, pengukuran suhu di dilakukan untuk mengontrol pemrosesan, penyimpanan atau reaksi kimia berjalan optimal pada industri. Permukaan (level) merupakan ketinggian permukaan cairan atau bahan di dalam sebuah wadah, level diukur untuk memastikan volume bahan dalam batas yang aman, level diukur untuk menghindari overfill atau kekurangan suatu bahan.
Selain aliran, tekanan, suhu dan level, terdapat variabel lain yang diukur dalam industri diantaranya : pH, kelembapan, konduktivitas, berat jenis, kandungan bahan mudah terbakar, kandungan oksigen, komposisi aliran kromatografi, emisi oksida nitrogen, kalorimetri dan lain-lain. Variabel-variabel ini dapat diukur secara langsung atau dianalisis di laboratorium, tergantung pada kebutuhan proses. Di industri pengolahan air limbah, pH diukur untuk memastikan air yang dibuang aman bagi lingkungan. Kelembapan pada bahan baku makanan seperti biji-bijian diukur untuk menjaga kualitas. Konduktivitas dalam industri kimia mengontrol konsentrasi bahan kimia, sementara berat jenis di industri minyak dan gas memonitor kualitas produk. Kandungan bahan mudah terbakar diukur di pembangkit listrik untuk efisiensi pembakaran, dan komposisi aliran kromatografi di industri kimia digunakan untuk memisahkan senyawa. Emisi oksida nitrogen diukur di industri otomotif untuk memenuhi standar lingkungan, dan kalorimetri di pembangkit listrik memastikan efisiensi bahan bakar yang digunakan.
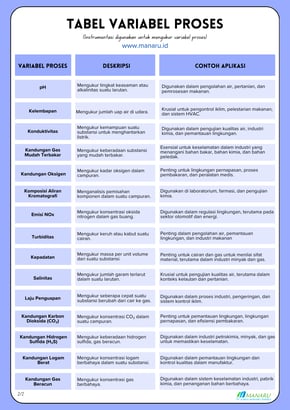

3. Flow Kerja Sistem Pengendalian Proses
Sistem pengendalian proses adalah suatu sistem yang dirancang untuk memantau dan mengontrol variabel-variabel yang ada dalam suatu proses industri agar tetap berada dalam kondisi yang diinginkan atau optimal. Sistem ini terdiri dari beberapa komponen utama yang bekerja secara berurutan dan terintegrasi, yaitu sensor/transducer, transmitter, controller, dan actuator. Setiap komponen memiliki peran yang sangat penting dalam memastikan sistem pengendalian dapat bekerja dengan baik.
Proses kerja pertama-tama dimulai dengan sensor yang mengukur variabel fisik (seperti tekanan, suhu, aliran, atau level) dari proses yang sedang berlangsung. Setelah sensor mendeteksi besaran fisik ini, informasi atau sinyal yang dihasilkan akan dikirimkan ke transducer. Transducer mengubah sinyal fisik ini (seperti sinyal listrik atau tekanan) menjadi sinyal yang dapat diproses lebih lanjut. Sinyal tersebut kemudian diteruskan ke transmitter, yang berfungsi untuk menguatkan atau mengolah sinyal agar dapat dikirim dengan akurat dan efektif ke controller. Sinyal yang diterima dari transmitter akan dibandingkan pada controller sesuai dengan nilai set point (nilai yang diinginkan atau target). Controller kemudian mengolah perbandingan ini untuk menghasilkan sinyal komando yang akan menginstruksikan actuator. Actuator, sebagai komponen terakhir dalam sistem, bertugas untuk mengubah variabel proses (seperti membuka atau menutup valve, mengatur kecepatan motor, atau merubah aliran gas) agar sesuai dengan perintah dari controller, dengan tujuan mengembalikan proses ke kondisi yang diinginkan.
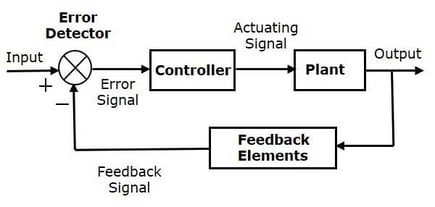
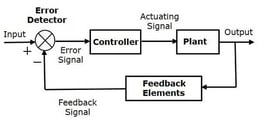
4. Komponen dalam Sistem Pengendalian Proses
Sensor dan Transduser
Sensor dan transduser berperan penting dalam mengukur variabel proses seperti suhu, level, aliran, dan tekanan di berbagai industri. Misalnya, untuk mengukur suhu, termokopel atau RTD (Resistance Temperature Detector) sering digunakan dalam industri kimia dan makanan untuk memastikan suhu tetap pada level yang diinginkan. Pengukuran level cairan, sensor level berbasis teknologi ultrasonik atau radar, seperti VegaWaves, digunakan di industri minyak dan gas untuk memantau tingkat bahan dalam tangki penyimpanan. Di sisi lain, sensor aliran seperti elektromagnetik flowmeter atau Coriolis mass flow meter digunakan dalam industri pengolahan air dan energi untuk mengukur laju aliran cairan atau gas dengan akurat. Sementara itu, sensor tekanan, seperti piezoelektrik atau strain gauge, dipasang pada pipa atau reaktor untuk memantau tekanan dan mencegah kebocoran atau kerusakan sistem, misalnya dalam pembangkit listrik atau industri minyak.
Setiap sensor ini menghasilkan sinyal yang diproses dan dikirimkan ke sistem kontrol untuk memastikan bahwa variabel proses tetap berada dalam batas yang aman dan optimal. Penggunaan sensor yang tepat memungkinkan pengukuran yang lebih akurat, sehingga membantu industri dalam mengendalikan proses dengan efisien, mengurangi risiko kecelakaan, dan memastikan kualitas produk yang tinggi.
Transmitter
Transmitter berfungsi untuk mengolah dan menguatkan sinyal yang diterima dari sensor, sehingga informasi yang diteruskan ke controller dapat diproses lebih lanjut. Misalnya, untuk pengukuran suhu, transmitter seperti Rosemount 3051S digunakan di industri kimia dan petrokimia untuk mengirimkan data suhu dari sensor RTD atau termokopel ke sistem kontrol. Dalam pengukuran level, transmitter seperti Endress+Hauser Prosonic dapat mengubah sinyal dari sensor ultrasonik menjadi format yang dapat dibaca oleh sistem kontrol untuk memantau level cairan atau material di tangki. Untuk aliran, transmitter seperti Yokogawa ROTAMASS memastikan data dari sensor Coriolis mass flow meter dikirimkan secara akurat ke pusat kontrol di industri minyak dan gas. Sedangkan dalam pengukuran tekanan, transmitter seperti Honeywell STT850 mengirimkan informasi tekanan yang diukur oleh sensor tekanan piezoelektrik ke sistem kontrol, memungkinkan pemantauan real-time dan pengendalian yang lebih baik di pabrik pembangkit listrik.
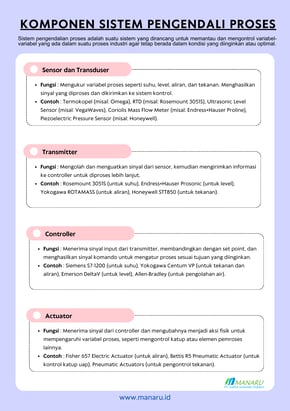
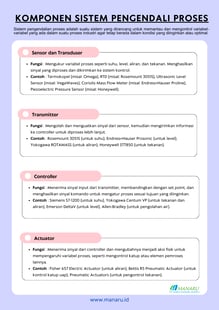
Controller
Controller berfungsi untuk menerima sinyal input dari transmitter, membandingkan nilai tersebut dengan set point yang telah ditetapkan, dan menghasilkan sinyal komando untuk mengatur proses sesuai dengan tujuan yang diinginkan. Dalam pengukuran suhu, controller seperti Siemens S7-1200 dapat menerima sinyal dari transmitter suhu dan mengontrol elemen pemanas atau pendingin untuk menjaga suhu tetap dalam rentang yang ditentukan, misalnya di reaktor kimia. Di industri minyak dan gas, controller seperti Yokogawa Centum VP digunakan untuk mengatur tekanan dan aliran, menerima sinyal dari transmitter tekanan dan aliran untuk memastikan proses tetap pada level yang aman dan optimal. Untuk level pengukuran, controller seperti Emerson DeltaV memproses data dari transmitter level dan mengatur pompa atau katup untuk mengendalikan volume cairan dalam tangki. Di industri pengolahan air, controller Allen-Bradley digunakan untuk mengatur level air di tangki, dengan memproses data dari transmitter level dan menyesuaikan kecepatan pompa untuk memastikan stabilitas level air.
Actuator
Actuator adalah komponen yang menerima sinyal dari controller dan mengubahnya menjadi aksi fisik untuk mempengaruhi variabel proses. Di industri, actuator sering digunakan untuk mengontrol berbagai parameter seperti suhu, tekanan, aliran, dan level. Sebagai contoh, di industri kimia, actuator elektrik seperti Fisher 657 digunakan untuk mengatur katup kontrol aliran berdasarkan sinyal yang diterima dari controller, mengontrol aliran cairan dalam pipa sesuai kebutuhan proses. Di sektor energi, actuator pneumatik seperti Bettis R5 digunakan untuk mengatur katup uap di pembangkit listrik, mengontrol aliran uap yang menuju turbin dengan membuka atau menutup katup sesuai instruksi dari controller untuk memastikan efisiensi operasional. Untuk pengukuran tekanan, actuator juga digunakan dalam sistem kontrol tekanan di industri minyak dan gas, seperti actuator pneumatik yang mengontrol katup safety valve untuk menjaga tekanan sistem tetap dalam batas aman. Top of Form
Kesimpulan
Instrumentasi dan pengendalian proses memainkan peran krusial dalam memastikan operasi industri berjalan efisien, aman, dan sesuai dengan standar yang ditetapkan. Melalui rangkaian komponen seperti sensor, transmitter, controller, dan actuator, sistem ini memungkinkan pemantauan dan pengaturan variabel proses seperti suhu, tekanan, aliran, dan level secara real-time. Penggunaan teknologi yang tepat di setiap komponen memungkinkan akurasi pengukuran dan pengendalian yang optimal, yang pada gilirannya meningkatkan efisiensi produksi, mengurangi risiko kecelakaan, dan menjaga kualitas produk di berbagai sektor industri, mulai dari kimia, energi, hingga pengolahan air.
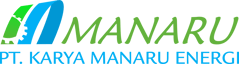
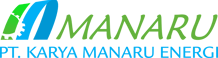
SOCIAL MEDIA
OFFICIAL STORE
We offer solutions to customers in need of quality equipment for the industry.
CATEGORY
Instrumentation
Valve
Fitting & Flange
Electrical
General Trading for Project
PT. Karya Manaru Energi
Kirana Two Office Tower, Lantai 10A, Jl. Boulevard Timur No.88
Pegangsaan Dua, Kelapa Gading, Jakarta Utara
DKI Jakarta - 12450
MARKETING OFFICE
© 2025 PT. Karya Manaru Energi.
All Right Reserved