Your Trusted Partner in Oil, Gas, Petrochemical, and Other Industrial Supplies
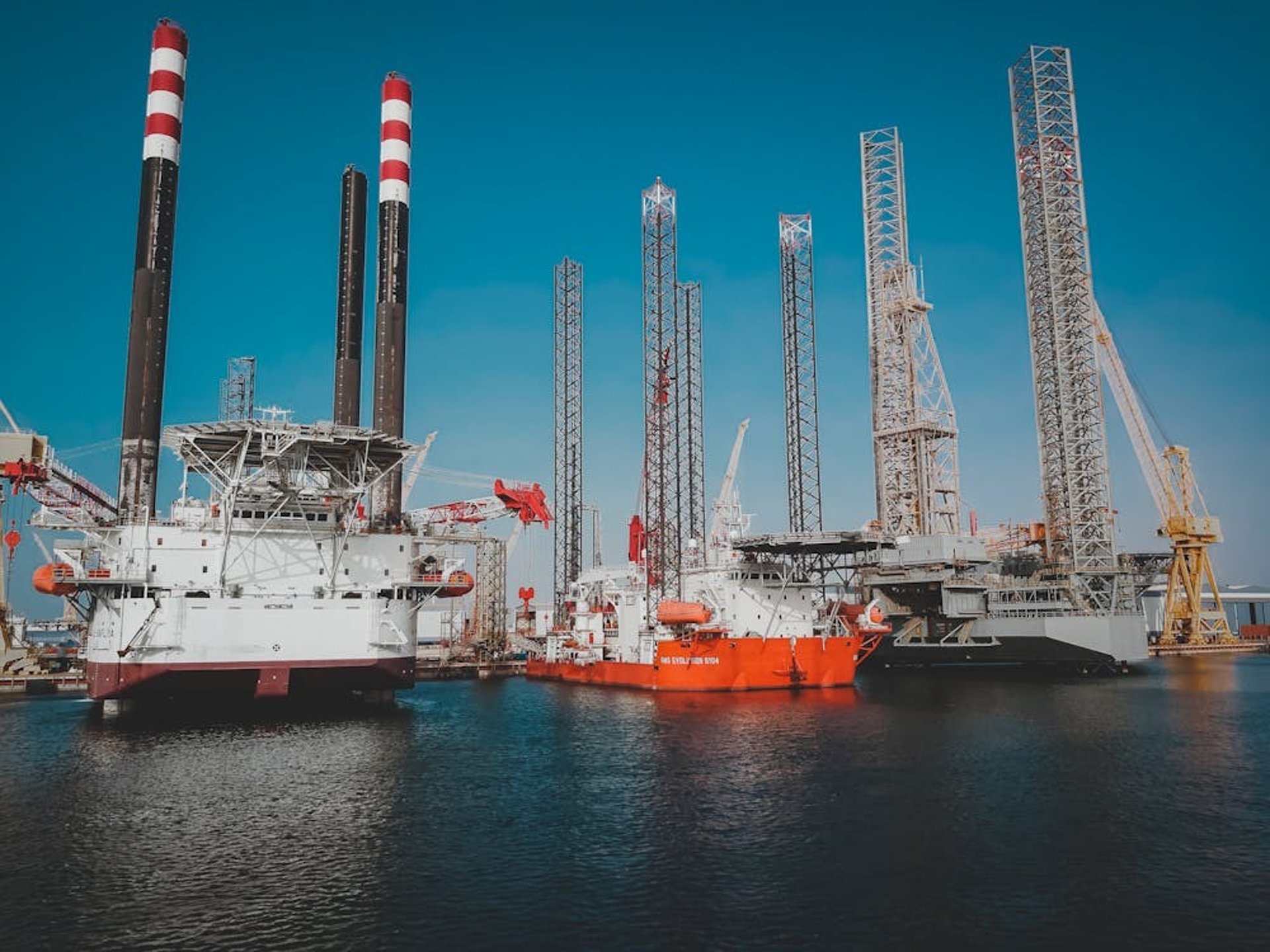
5 Langkah Memilih Valve yang Tepat untuk Aplikasi Industri
Pemilihan valve yang tepat sangat berpengaruh pada kinerja keseluruhan sistem, mulai dari efisiensi energi, keandalan operasi, hingga keselamatan kerja. Salah memilih valve dapat mengakibatkan kerugian finansial yang signifikan, seperti kebocoran, kegagalan sistem, atau kerusakan pada peralatan yang lebih kompleks.
11/16/20248 min read
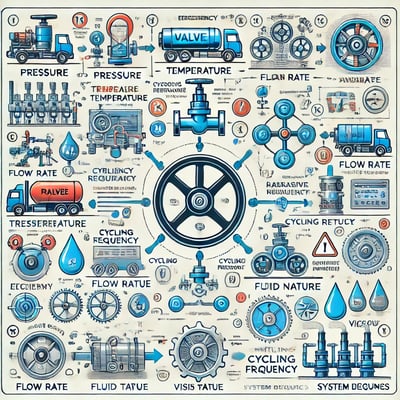
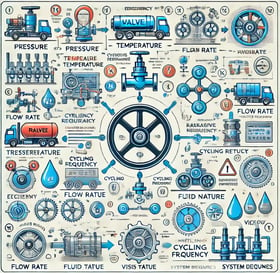
Valve merupakan komponen vital dalam sistem industri yang berfungsi untuk mengatur, mengendalikan, dan mengarahkan aliran fluida—baik gas, cairan, maupun campuran—dalam sistem perpipaan dan peralatan. Selain berperan dalam membuka atau menutup aliran, valve juga memiliki fungsi penting dalam mengatur tekanan, mengontrol laju aliran, dan memodifikasi kondisi fluida sesuai dengan kebutuhan operasional. Dalam operasional industri, valve bertindak sebagai pengendali yang memastikan sistem bekerja secara efisien dan aman. Tanpa valve yang tepat, pengendalian proses produksi menjadi sangat sulit, berisiko menyebabkan gangguan operasional, pemborosan energi, serta kerusakan pada peralatan yang lebih mahal.
Pemilihan valve yang tepat sangat berpengaruh pada kinerja keseluruhan sistem, mulai dari efisiensi energi, keandalan operasi, hingga keselamatan kerja. Salah memilih valve dapat mengakibatkan kerugian finansial yang signifikan, seperti kebocoran, kegagalan sistem, atau kerusakan pada peralatan yang lebih kompleks. Oleh karena itu, memilih valve yang sesuai dengan karakteristik fluida dan kebutuhan aplikasi sangat penting untuk mengoptimalkan proses operasional di berbagai sektor industri, termasuk minyak dan gas, kimia, pembangkit listrik, dan lainnya. Dengan pemilihan yang tepat, industri dapat memastikan kelancaran operasional dan mengurangi risiko kerugian serta meningkatkan keandalan dan efisiensi secara keseluruhan.
Untuk mencapai hal ini, terdapat lima langkah strategis yang perlu diperhatikan dalam memilih valve yang tepat untuk aplikasi industri. Langkah-langkah ini dirancang untuk memastikan bahwa valve yang dipilih tidak hanya memenuhi standar teknis, tetapi juga memberikan manfaat jangka panjang dalam hal efisiensi operasional dan keandalan sistem. Berikut adalah lima langkah tersebut:
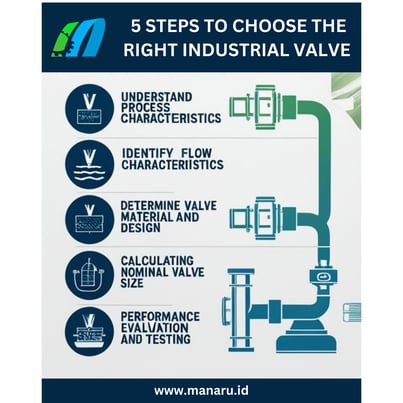
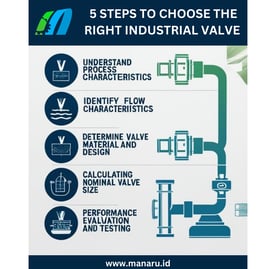
1. Memahami Karakteristik Proses
Langkah pertama dalam memilih valve yang tepat adalah dengan memahami kondisi operasional yang ada di lapangan, seperti tekanan kerja, suhu fluida, dan jenis fluida yang akan mengalir melalui sistem. Setiap faktor ini memengaruhi pilihan bahan dan desain valve yang digunakan. Misalnya, suhu yang sangat rendah atau tinggi membutuhkan material khusus untuk mencegah kerusakan atau kegagalan struktural pada valve. Selain itu, jenis fluida, seperti gas atau cairan yang bersifat korosif atau abrasif, memerlukan ketahanan bahan terhadap kerusakan akibat reaksi kimia atau gesekan.
Sebagai contoh, dalam pabrik LNG (Liquid Natural Gas) yang menangani gas metana cair pada suhu sangat rendah, sekitar -162°C, diperlukan penggunaan cryogenic valve. Cryogenic valve, yang biasanya terbuat dari bahan seperti stainless steel 316L, dirancang khusus untuk tetap stabil dan berfungsi dengan baik pada suhu ekstrem tersebut. Di sisi lain, pada sistem uap superheated di pembangkit listrik yang beroperasi pada suhu tinggi, sekitar 540°C, dan tekanan sangat tinggi, yaitu 150 bar, diperlukan bahan seperti P91 pada globe valve. Bahan ini memiliki ketahanan yang lebih baik terhadap perubahan bentuk (deformasi) pada suhu tinggi, yang dapat menghindari risiko kebocoran atau kegagalan sistem. Dengan pemilihan material yang tepat sesuai kondisi operasional, valve akan berfungsi dengan optimal dan memiliki umur pakai yang lebih lama.
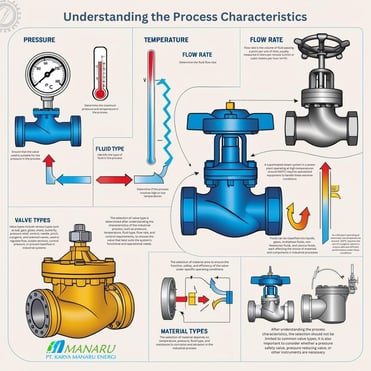
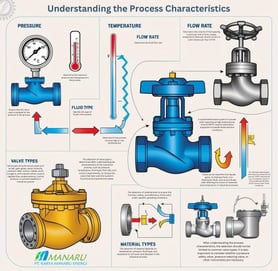
2. Mengidentifikasi Karakteristik Aliran
Langkah kedua dalam memilih valve yang tepat adalah dengan mengidentifikasi pola aliran fluida yang ada dalam sistem. Pola aliran ini dapat dibagi menjadi tiga jenis utama: aliran turbulen, aliran laminar, dan aliran campuran. Pemahaman terhadap jenis aliran ini sangat penting karena setiap jenis aliran mempengaruhi kinerja valve secara langsung, terutama dalam hal pengendalian aliran dan efisiensi operasional.
Aliran Turbulen terjadi ketika fluida mengalir dengan kecepatan tinggi dan turbulensi yang menyebabkan pola aliran menjadi kacau. Pada aliran turbulen, partikel-partikel fluida bergerak secara acak dan membentuk pusaran di dalam pipa. Aliran ini biasanya ditemukan pada sistem dengan tekanan tinggi dan laju aliran besar, seperti dalam sistem distribusi air bersih. Dalam kondisi ini, butterfly valve sering dipilih karena desainnya yang sederhana dan efisien. Butterfly valve memiliki cakram datar yang diputar untuk mengatur aliran, yang memungkinkan kontrol aliran besar dengan kerugian tekanan minimal. Penggunaan butterfly valve pada aliran turbulen juga disebabkan oleh bentuknya yang kompak, yang memungkinkan pemasangan dalam ruang terbatas tanpa mengurangi efisiensi. Sebagai contoh, pada sistem distribusi air bersih yang beroperasi dengan tekanan rendah dan aliran turbulen, butterfly valve dapat mengontrol aliran dengan sangat efisien, menjaga stabilitas aliran tanpa memberikan hambatan yang berarti.
Aliran Laminar, di sisi lain, terjadi pada fluida yang mengalir dengan kecepatan rendah dan aliran yang halus. Dalam aliran laminar, partikel fluida bergerak sejajar dalam lapisan-lapisan tanpa banyak gangguan. Aliran ini lebih sering terjadi pada sistem dengan fluida kental atau viskositas tinggi. Pada kondisi ini, ball valve sering digunakan karena desainnya yang memungkinkan aliran fluida yang stabil dan minim hambatan. Ball valve memiliki bola berputar di dalamnya yang memiliki lubang yang dapat disesuaikan untuk mengontrol laju aliran. Ball valve sangat efektif dalam mengontrol aliran pada fluida dengan viskositas tinggi, seperti dalam pengolahan bahan kimia atau industri makanan dan minuman, di mana fluida yang digunakan memiliki kekentalan yang lebih tinggi dan memerlukan pengendalian aliran yang lebih presisi tanpa menambah hambatan yang signifikan. Dalam sistem seperti itu, ball valve dapat menjaga aliran tetap stabil tanpa mempengaruhi tekanan secara besar.
Aliran Campuran terjadi ketika aliran fluida terdiri dari campuran antara laminar dan turbulen, sering ditemukan pada sistem dengan variasi kecepatan aliran dan tekanan. Pada aplikasi aliran campuran, pemilihan valve harus mempertimbangkan karakteristik kedua jenis aliran ini. Dalam hal ini, valve yang dapat memberikan kontrol yang lebih halus dan lebih efisien, seperti globe valve, sering dipilih untuk mengatur aliran pada kondisi ini. Globe valve memiliki desain yang memungkinkan pengaturan aliran dengan presisi tinggi dan umumnya digunakan untuk aplikasi yang membutuhkan kontrol aliran yang lebih detil pada berbagai kondisi aliran fluida.
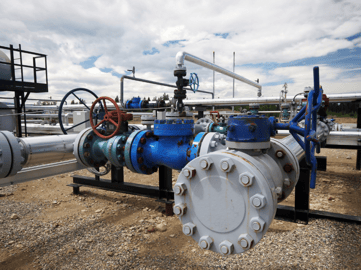
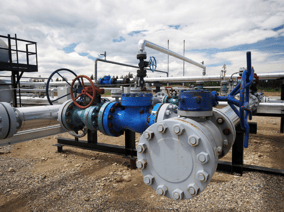
3. Menentukan Material dan Desain Valve
Memilih material valve yang sesuai sangat penting untuk menjamin ketahanan terhadap kondisi operasional, termasuk suhu, tekanan, dan sifat kimia fluida. Setiap material memiliki kekuatan dan kelemahannya masing-masing, serta tingkat ketahanannya terhadap korosi atau abrasi. Oleh karena itu, pemilihan material valve yang tepat akan menghindari kegagalan prematur dan meningkatkan umur pakai valve.
Sebagai contoh, dalam sistem transportasi asam sulfat dengan konsentrasi tinggi, seperti pada pipa di industri kimia, pemilihan valve berbahan Hastelloy C-276 sangat krusial. Material ini memiliki ketahanan luar biasa terhadap korosi yang disebabkan oleh asam sulfat yang agresif, yang tidak dapat ditangani oleh stainless steel biasa. Di sisi lain, dalam aplikasi seperti sistem pemadam kebakaran yang menggunakan air laut, valve berbahan perunggu atau monel lebih disukai karena ketahanannya terhadap korosi akibat garam.
4. Menghitung Ukuran Nominal Valve (Sizing)
Langkah 4 dalam memilih valve yang tepat adalah melakukan perhitungan sizing atau penentuan ukuran nominal valve. Pemilihan ukuran yang tepat sangat penting karena jika ukuran valve terlalu kecil (under-sizing) atau terlalu besar (over-sizing), keduanya dapat memengaruhi efisiensi sistem secara signifikan. Over-sizing atau pemilihan valve dengan ukuran yang lebih besar dari yang diperlukan dapat menyebabkan pengaturan aliran menjadi kurang akurat, mengurangi kemampuan kontrol aliran, dan meningkatkan biaya operasional akibat pemborosan energi. Sebaliknya, under-sizing valve akan menghambat aliran fluida, meningkatkan tekanan diferensial, dan membebani pompa serta komponen lainnya, yang dapat mengurangi efisiensi dan memperburuk kinerja sistem.
Perhitungan sizing valve memerlukan analisis beberapa faktor, seperti laju aliran fluida, tekanan diferensial, jenis fluida, serta karakteristik sistem lainnya. Misalnya, dalam sistem pendinginan di kilang minyak dengan aliran air sebesar 100 m³/jam dan tekanan diferensial 1 bar, perhitungan sizing menunjukkan bahwa valve dengan ukuran DN100 adalah pilihan yang optimal. Jika valve yang digunakan terlalu kecil (under-sized), seperti DN80, maka akan terjadi peningkatan tekanan diferensial, membebani pompa, dan menurunkan efisiensi. Di sisi lain, over-sizing valve menjadi DN120 akan membuat kontrol aliran menjadi kurang presisi, mengurangi kemampuan valve untuk mengatur aliran dengan baik, dan dapat mengakibatkan ketidakstabilan proses.
Contoh lain bisa ditemukan dalam aplikasi distribusi gas di industri, di mana aliran gas mencapai 5000 Nm³/jam dengan tekanan diferensial 5 bar. Jika valve yang dipilih terlalu kecil (under-sized), seperti DN80, maka valve tersebut akan kesulitan menangani volume gas yang besar, menyebabkan penurunan tekanan yang signifikan dan mengganggu operasi. Sebaliknya, jika valve yang digunakan terlalu besar (over-sized), seperti DN150, meskipun aliran dapat berjalan dengan lancar, over-sizing ini akan mengurangi ketepatan kontrol tekanan dan aliran, serta membuat sistem pengaturan lebih sulit untuk menjaga kestabilan.
Dengan demikian, perhitungan sizing valve yang cermat sangat penting untuk menjaga efisiensi dan kestabilan sistem. Memilih ukuran valve yang tepat membantu menghindari over-sizing yang dapat menambah biaya operasional serta memastikan aliran fluida terkontrol dengan baik sesuai kebutuhan sistem.
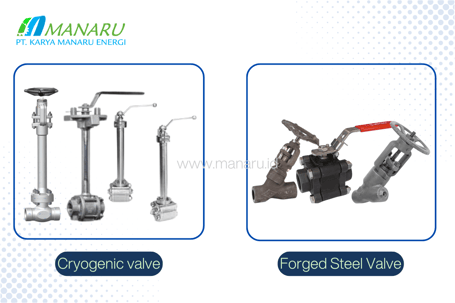
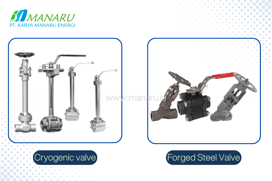
5. Evaluasi Kinerja dan Uji Coba
Setelah pemilihan valve yang tepat dan pemasangannya selesai, tahap penting selanjutnya adalah melakukan evaluasi kinerja dan pengujian di lapangan. Proses ini bertujuan untuk memastikan bahwa valve yang telah dipasang berfungsi secara optimal dalam kondisi operasional yang sebenarnya. Evaluasi dan uji coba ini sangat krusial karena dapat mengidentifikasi masalah potensial lebih awal, menghindari gangguan operasional, serta memastikan sistem berfungsi secara efisien dan aman.
Kinerja valve harus dievaluasi berdasarkan beberapa parameter penting seperti laju aliran, kestabilan tekanan, serta respon valve terhadap perintah operasional. Salah satu indikator kunci dalam evaluasi kinerja adalah memantau fluktuasi tekanan dan aliran di sepanjang sistem. Sebagai contoh, dalam aplikasi transportasi gas alam dengan tekanan operasi 20 bar, penting untuk memastikan bahwa valve tidak menyebabkan fluktuasi tekanan yang berlebihan, yang dapat merusak peralatan dan mengganggu operasi. Pengujian dilakukan dengan memantau perubahan tekanan pada berbagai titik dalam sistem dan memastikan bahwa fluktuasi tekanan berada dalam batas yang dapat diterima, misalnya ±1%. Jika hasil pengujian menunjukkan fluktuasi tekanan yang lebih besar, ini dapat mengindikasikan bahwa valve atau aktuator yang digunakan tidak sesuai dengan karakteristik sistem dan perlu dilakukan penyesuaian.
Uji coba lapangan dilakukan untuk memverifikasi bahwa valve bekerja sesuai dengan spesifikasi teknis dan di bawah kondisi yang dihadapi di dunia nyata. Pada tahap ini, valve diuji untuk mengidentifikasi masalah potensial yang mungkin tidak terdeteksi saat proses desain dan pemasangan. Hal ini termasuk menguji apakah valve dapat menangani variasi suhu atau tekanan ekstrem yang mungkin terjadi selama operasi. Misalnya, dalam aplikasi industri kimia dengan fluida korosif atau bertekanan tinggi, uji coba untuk memastikan bahwa valve tidak mengalami kebocoran, deformasi, atau kerusakan yang dapat membahayakan sistem sangat penting. Uji coba ini sering melibatkan pemeriksaan kebocoran pada segel atau sambungan, memverifikasi bahwa aktuator berfungsi dengan baik untuk membuka atau menutup valve sesuai dengan perintah, serta memeriksa respon valve terhadap perubahan aliran.
Selama proses evaluasi, sangat penting untuk memeriksa apakah aktuator yang terpasang bekerja dengan baik dalam menggerakkan valve sesuai dengan kebutuhan proses. Tuning aktuator dapat dilakukan untuk memastikan waktu respons yang tepat dan memastikan bahwa valve beroperasi dengan presisi. Kadang-kadang, meskipun valve telah dipilih dengan benar, aktuatornya mungkin memerlukan penyesuaian untuk meningkatkan kinerjanya atau mengatasi masalah ketidaksesuaian dengan karakteristik aliran atau tekanan sistem.
Selain itu, selama evaluasi dan pengujian, jika ditemukan masalah yang berulang atau ketidaksesuaian dalam kinerja valve, penyesuaian atau penggantian valve mungkin diperlukan. Misalnya, jika valve terlalu sering mengalami kegagalan atau kebocoran, ini bisa menjadi indikasi bahwa tipe atau ukuran valve yang digunakan tidak sesuai dengan kondisi operasional. Dalam situasi seperti ini, penggantian valve dengan model yang lebih sesuai atau material yang lebih tahan terhadap kondisi ekstrem bisa menjadi solusi terbaik.
Kesimpulan
Kesimpulannya, pemilihan valve yang tepat sangat krusial dalam aplikasi industri untuk memastikan efisiensi, keandalan, dan keselamatan sistem. Proses ini dimulai dengan memahami karakteristik proses, seperti suhu, tekanan, dan jenis fluida yang mengalir, agar dapat memilih material dan desain valve yang sesuai. Selain itu, penting untuk mengidentifikasi karakteristik aliran, apakah turbulen, laminar, atau campuran, untuk menentukan jenis valve yang tepat dalam mengendalikan aliran secara efisien. Pemilihan material yang tepat juga sangat mempengaruhi ketahanan valve terhadap kondisi operasional yang ekstrem. Ukuran nominal valve yang tepat harus dihitung dengan cermat untuk memastikan kinerja yang optimal tanpa mengorbankan efisiensi sistem. Terakhir, evaluasi kinerja dan uji coba lapangan sangat diperlukan untuk memastikan valve dapat berfungsi dengan baik di kondisi nyata dan memenuhi spesifikasi yang diinginkan. Dengan mengikuti langkah-langkah ini, industri dapat mengoptimalkan kinerja sistem, mengurangi risiko kerusakan, dan meningkatkan efisiensi serta keamanan dalam jangka panjang.
Baca Juga
10 Kesalahan Umum dalam Pemasangan Instrumen yang Harus Dihindari di Industri Minyak, Gas, dan Petrokimia
Kontrol Valve Pintar: Inovasi untuk Proses Industri Yang Lebih Efisien dan Aman
Material Pipa Terbaik untuk Industri Kimia: Mengapa Stainless Steel Bukan Satu-satunya Pilihan Utama?
Remote Valve Operation : Rahasia di Balik Keamanan Industri
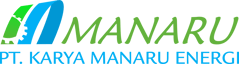
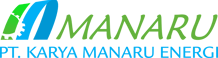
SOCIAL MEDIA
OFFICIAL STORE
We offer solutions to customers in need of quality equipment for the industry.
CATEGORY
Instrumentation
Valve
Fitting & Flange
Electrical
General Trading for Project
PT. Karya Manaru Energi
Kirana Two Office Tower, Lantai 10A, Jl. Boulevard Timur No.88
Pegangsaan Dua, Kelapa Gading, Jakarta Utara
DKI Jakarta - 12450
MARKETING OFFICE
© 2025 PT. Karya Manaru Energi.
All Right Reserved